تست مخرب و غیرمخرب جوش
تست مخرب (DT) قطعه را به نحوی از بین میبرد یا تغییر میدهد طوری که حتی اگر تست را پشت سر بگذارد دیگر برای استفاده مناسب نمیباشد. انواع تست غیر مخرب (NDT) قطعه را خراب و تخریب نمیکند یا تغییر نمیدهد تا در صورت موفقیت در تست، همچنان برای سرویس مناسب باشد. در حین بررسی کلی این تفاوتها، به خاطر داشته باشید که DT و NDT به طور کلی برای اهداف متفاوتی استفاده میشوند.
در حالیکه تست مخرب را میتوان برای تجزیه و تحلیل شکست استفاده کرد، اما بر اطمینان از کیفیت اقلام، قبل از تولید انبوه تمرکز دارد. تستهای غیرمخرب بر روی قطعات در حال کار انجام میشود تا علائم تخریب اولیه را شناسایی کرده و از خرابی تجهیزات جلوگیری کند. آنها به تیمهای تعمیر و نگهداری کمک میکنند تا تعمیر و نگهداری مبتنی بر شرایط و تعمیر و نگهداری پیش بینی را انجام دهند. در ادامه با پله همراه باشید تا بیشتر با تستهای جوش آشنا شوید.
تست غیرمخرب (NDT) چیست؟
تست غیرمخرب (NDT) یک تکنیک تست و تجزیه و تحلیل است که توسط صنعت برای ارزیابی خواص یک ماده، جزء، ساختار یا سیستم برای عیوب و ناپیوستگیهای جوشکاری بدون آسیب رساندن به قطعه اصلی استفاده میشود. NDT همچنین به عنوان معاینه و ارزیابی غیرمخرب (NDE) و بازرسی غیرمخرب (NDI) شناخته میشود.
روش های تست غیرمخرب
روش های تست NDT فعلی عبارتند از:
تست آکوستیک امیشن (AE)
این یک تکنیک NDT است که بر تشخیص انفجارهای کوتاه اولتراسوند ساطع شده توسط ترکهای فعال تحت بار تکیه دارد. تست AE که اغلب یک روش نظارت مستمر سلامت سازه (SHM) میباشد که برای همه تجهیزات کاریرد دارد به عنوان مثال برای مخازن تحت فشار، مخازن اتمسفریک، راکتورها، خطوط لوله، روی پل ها و …. که نشتی و خوردگی فعال نیز توسط AE قابل تشخیص هستند.
تست الکترومغناطیسی (ET)
این روش تست از جریان الکتریکی یا میدان مغناطیسی استفاده میکند که از یک قسمت رسانا عبور میکند. سه نوع آزمایش الکترومغناطیسی شامل آزمایش جریان گردابی، اندازهگیری میدان جریان متناوب (ACFM) و آزمایش میدان از راه دور (RFT) وجود دارد. آزمایش جریان گردابی از یک سیم پیچ جریان متناوب برای القای میدان الکترومغناطیسی به قطعه آزمایش استفاده میکند. اندازهگیری میدان متناوب و آزمایش میدان از راه دور هر دو از یک پروب برای معرفی یک میدان مغناطیسی استفاده میکنند و RFT معمولاً برای آزمایش لولهها استفاده میشود.
تست نشت (LT)
آزمایش نشت را میتوان به چهار روش مختلف تقسیم کرد:
نشت حباب
تغییر فشار
دیود هالوژن
طیف سنج جرمی
آزمایش نشت حباب از یک مخزن مایع یا محلول صابون برای قطعات بزرگتر برای تشخیص گاز (معمولاً هوا) که از قطعه آزمایش به شکل حباب نشت میکند، استفاده میکند. فقط در سیستمهای بسته استفاده میشود.
آزمایش تغییر فشار از فشار یا خلاء برای نظارت بر قطعه آزمایش استفاده میکند. از دست دادن فشار یا خلاء در یک بازه زمانی مشخص نشان میدهد که نشتی در سیستم وجود دارد.
آزمایش دیود هالوژن همچنین از فشار برای یافتن نشتی استفاده میکند. به جز در این مورد، هوا و یک گاز ردیاب مبتنی بر هالوژن با هم مخلوط میشوند و یک واحد تشخیص دیود هالوژن برای تعیین محل نشتی استفاده میشود.
آزمایش طیفسنج جرمی از هلیوم یا ترکیب هلیوم و هوا در داخل یک محفظه آزمایشی برای تشخیص هرگونه تغییر در نمونه هوا استفاده میشود که نشاندهنده نشتی است. در روش دیگر، میتوان از خلاء استفاده کرد، در این صورت طیف سنج جرمی از محفظه خلاء نمونهبرداری میکند تا هلیوم یونیزهشده را تشخیص دهد، که نشان میدهد نشت وجود داشتهاست.
نشت شار مغناطیسی (MFL)
این روش از یک آهنربای قدرتمند برای ایجاد میدانهای مغناطیسی استفاده میکند، سپس از یک سنسور برای تشخیص تغییرات در چگالی شار مغناطیسی استفاده میشود که هرگونه کاهش در مواد را به دلیل حفره، فرسایش یا خوردگی نشان میدهد که برای سازههای فولادی مانند خطوط لوله و مخازن ذخیره هم کاربرد دارد.
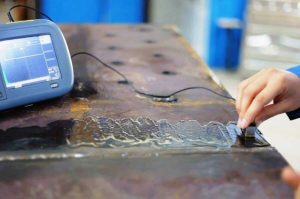
تست UT
تست غیر مخرب UT یا تست التراسونیک یکی از رایج ترین روش های غیر مخرب برای شناسایی عیوب داخلی در مواد مختلف، به خصوص فلزات، می باشد. این روش بر اساس پالس امواج التراسونیک و انعکاس آنها از عیوب عمل می کند.
مراحل انجام تست UT:
آماده سازی سطح: قبل از شروع تست، سطح مورد نظر باید تمیز و عاری از هرگونه آلودگی، چربی، رطوبت و رنگ باشد.
اعمال ژل: یک لایه نازک از ژل بین مبدل و سطح مورد آزمایش اعمال می شود تا امواج التراسونیک به طور کامل به داخل ماده منتقل شوند.
فرستادن امواج التراسونیک: مبدل امواج التراسونیک را به داخل ماده ارسال می کند.
دریافت امواج التراسونیک: گیرنده امواج التراسونیک منعکس شده از عیوب را دریافت می کند.
تجزیه و تحلیل نتایج: با توجه به زمان رفت و برگشت امواج و دامنه ی سیگنال دریافتی، می توان موقعیت، اندازه و نوع عیب را تعیین کرد.
کاربرد های تست UT:
انواع بازرسی جوشکاری: برای شناسایی ترک ها، حفره ها و سایر عیوب در جوش ها
بازرسی لوله ها و مخازن: برای شناسایی ترک ها، حفره ها، خوردگی و فرسایش در لوله ها و مخازن
انواع بازرسی قطعات صنعتی: برای شناسایی ترک ها، حفره ها، تخلخل ها و ناپیوستگی ها در قطعات صنعتی مانند توربین ها، ژنراتورها و مبدل های حرارتی
بازرسی سازه های هوایی: برای شناسایی ترک ها، خوردگی و فرسایش در سازه های هوایی مانند بال ها، بدنه و موتور هواپیما
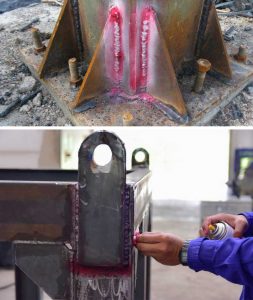
تست مایع نافذ(PT)
تست مایع نافذ شامل اعمال یک سیال با ویسکوزیته کم به ماده مورد آزمایش است. این مایع قبل از اعمال یک توسعه دهنده به هرگونه نقصی مانند ترک یا تخلخل نفوذ میکند که به مایع نافذ اجازه میدهد تا به سمت بالا نفوذ کند و نشانه قابل مشاهدهای از نقص ایجاد کند. تستهای مایع نافذ را میتوان با استفاده از مواد نافذ قابل جابجایی با حلال، نافذهای قابل شستشو با آب انجام داد.
مراحل انجام تست PT:
آماده سازی سطح: قبل از شروع تست، سطح مورد نظر باید تمیز و عاری از هرگونه آلودگی، چربی، رطوبت و رنگ باشد.
اعمال مایع نافذ: مایع نافذ به روش های مختلفی مانند اسپری کردن، غوطه وری یا قلم مو زدن به سطح اعمال می شود.
زمان دهی: به مایع نافذ زمان کافی داده می شود تا به داخل ترک ها و حفره ها نفوذ کند.
حذف مایع نافذ اضافی: مایع نافذ اضافی از روی سطح با استفاده از حلال یا روش های دیگر شسته می شود.
اعمال ماده آشکارساز: ماده آشکارساز به سطح اعمال می شود تا مایع نافذ محبوس شده در ترک ها و حفره ها را جذب کند.
بررسی و تفسیر نتایج: پس از خشک شدن ماده آشکارساز، سطح مورد نظر از نظر وجود ترک ها و حفره ها با چشم غیر مسلح یا با استفاده از تجهیزات اپتیکی مانند ذره بین یا لوپ بررسی می شود.
مزایا
سادگی و سهولت انجام: این تست به تجهیزات و مهارت پیچیده ای نیاز ندارد و به راحتی قابل انجام است.
حساسیت بالا: این تست می تواند ترک ها و حفره های بسیار ریز را نیز شناسایی کند.
قابلیت استفاده برای طیف وسیعی از مواد: این تست می تواند برای انواع مختلف فلزات، آلیاژها و برخی از مواد غیر فلزی مانند سرامیک ها و پلاستیک ها استفاده شود.
قیمت مناسب: این تست در مقایسه با سایر روش های NDT از نظر اقتصادی مقرون به صرفه تر است.
معایب
عدم توانایی در شناسایی عیوب داخلی: این تست فقط می تواند عیوب سطحی را شناسایی کند و برای بررسی عیوب داخلی مانند ترک های زیر سطحی مناسب نیست.
نیاز به تمیز کاری دقیق: سطح مورد آزمایش باید قبل از انجام تست به طور کامل تمیز شود، در غیر این صورت ممکن است نتایج تست با خطا همراه باشد.
حساسیت به برخی از مواد: برخی از مواد شیمیایی موجود در مایع نافذ و ماده آشکارساز می توانند برای سلامتی مضر باشند و باید با احتیاط از آنها استفاده شود.
جوشکاری و آشنایی با انواع روشها و تکنیکها
اصول و روشهای تعمیر و نگهداری ساختمان
کاربردهای تست PT:
انواع بازرسی جوشکاری: برای شناسایی ترک ها و حفره ها در جوش ها
بازرسی قطعات ریخته گری و فورج: برای شناسایی ترک ها، حفره ها و سایر عیوب در قطعات ریخته گری و فورج
انواع بازرسی لوله ها و مخازن: برای شناسایی ترک ها، حفره ها و خوردگی در لوله ها و مخازن
بازرسی سازه های فلزی: برای شناسایی ترک ها، حفره ها و خوردگی در سازه های فلزی مانند پل ها، ساختمان ها و دکل ها
تست های مخرب و غیر مخرب از لحاظ هزینه و زمان تفاوت های زیادی دارند که این اصل در سرعت و پیشرفت پروژه بسیار حائز اهمیت می باشد.
تست ذرات مغناطیسی (MT)
این فرآیند NDT از میدانهای مغناطیسی برای یافتن ناپیوستگیها در سطح یا نزدیک سطح مواد فرومغناطیسی استفاده میکند. میدان مغناطیسی را میتوان با یک آهنربای دائمی یا یک آهنربای الکتریکی ایجاد کرد که برای اعمال جریان نیاز به یک جریان دارد. میدان مغناطیسی هرگونه ناپیوستگی را مشخص میکند زیرا خطوط شار مغناطیسی نشتی ایجاد میکنند که با استفاده از ذرات مغناطیسی که به داخل ناپیوستگی کشیدهمیشوند قابل مشاهدهاست.
مراحل انجام تست MT:
آماده سازی سطح: قبل از شروع تست، سطح مورد نظر باید تمیز و عاری از هرگونه آلودگی، چربی، رطوبت و رنگ باشد.
مغناطیسی کردن قطعه: قطعه با استفاده از جریان الکتریکی یا آهنربای دائمی مغناطیسی می شود.
اعمال ذرات مغناطیسی: ذرات مغناطیسی به روش های مختلفی مانند پاشیدن، غوطه وری یا الکترواستاتیک به سطح اعمال می شوند.
بررسی و تفسیر نتایج: ذرات مغناطیسی در محل عیوب تجمع پیدا می کنند و الگویی را بر روی سطح ایجاد می کنند که با چشم غیر مسلح یا با استفاده از تجهیزات اپتیکی مانند ذره بین یا لوپ قابل مشاهده است.
تست MT در کنار سایر روش های NDT مانند تست التراسونیک، تست رادیوگرافی و تست PT، ابزاری ارزشمند برای ارزیابی کیفیت و سلامت مواد و سازه ها می باشد.
انتخاب روش NDT مناسب به عوامل مختلفی از جمله نوع ماده، نوع سازه، الزامات کیفی و بودجه پروژه بستگی دارد. تست های مخرب و غیر مخرب باید توسط آزمایشگاه های خیلی مجهز و معتبر صورت بگیرد.
رادیوگرافی (RT= Radiographic Test)
رادیوگرافی تست غیر مخرب دیگری است که برای کنترل کیفی قطعات استفاده میشود. این تست علاوهبر آنالیز سطحی قابلیت تشخیص نقایص قطعه تا عمق مشخصی را هم دارد. برای انجام این تست از اشعه ایکس یا گاما استفاده میشود. به دلیل تغییر ماهیت ماده در نقایص خواص موج تابشی تغییر میکند و با دریافت بازیافت آن اطلاعات مربوط به نقایص استخراج میشود.
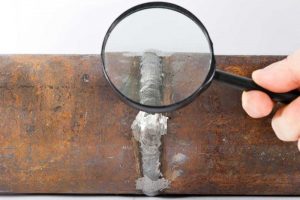
بازرسی چشمی (VT= Visual Test)
بازرسی چشمی بدویترین نوع کنترل کیفی مواد است که در آن با دقت پایینی میتوان عیوب سطحی قطعات را بررسی کرد. به عبارت دیگری برخی از عیوب را به طور واضح میتوان با چشم تشخیص داد. و رد شدن قطعه با این تست، از هزینه اضافه تستهای غیر مخرب بعدی جلوگیری میکند. البته عوامل مختلفی در این روش تاثیرگذار است. خستگی بازرس، تجربه، نور و زاویه دید بر تشخیص عیوب با این روش موثر میباشد.
مزایای استفاده از NDT چیست؟
تعدادی مزیت متمایز وجود دارد که بارزترین آنها این است که قطعات مورد آزمایش در اثر این فرآیند آسیبی نبینند و در صورت یافتن هر گونه مشکل، به جای تعویض یک مورد، امکان تعمیر آن وجود دارد. همچنین یک روش تست بسیار ایمن برای اپراتورها است. اگرچه برخی از انواع آزمایش – مانند آزمایش رادیوگرافی – هنوز باید تحت شرایط سخت انجام شوند. این تکنیک تست همچنین میتواند با اطمینان از ایمن بودن سازهها، اجزاء و ماشین آلات به جلوگیری از آسیب یا مرگ و میر کمک کند.
تست مخرب چیست؟
تست مخرب (اغلب به اختصار DT ) روش آزمایشی است که برای یافتن نقطه دقیق خرابی مواد، قطعات یا ماشینها انجام میشود. در طول فرآیند مورد آزمایششده، تحت فشار قرار میگیرد که در نهایت باعث تغییر شکل یا تخریب مواد میشود. به طور طبیعی، قطعات و مواد آزمایششده را نمیتوان پس از انجام مراحل تست مخرب در عملیات عادی استفاده مجدد کرد. آزمایشات مخرب معمولاً قبل از ورود یک قطعه به تولید انبوه انجام میشود. OEMها (Original equipment manufacturer) باید محدودیتهای محصولات خود را بدانند تا توصیههای مناسبی برای نگهداری و عملکرد ماشینهای خود ارائه دهند.
چه کسی تست های مخرب را انجام میدهد؟
تست های مخرب توسط محققان، دانشمندان و تکنسین های متخصص انجام میشود. اینکه چه کسی آن را انجام میدهد با توجه به نوع آزمایش مخربی که باید انجام شود مشخص میشود. به طور کلی، تست مخرب توسط:
دانشمندان مواد
مهندسین متالورژی و پلیمر
کارشناسان شیمی و فرآیندهای الکتروشیمیایی
کارشناسان تحلیل شکست
تحلیلگران کنترل کیفیت
کارشناسان رعایت مقررات
تست مخرب جوش
روش تست مخرب جوش DT نیز یکی دیگر از انواع تست جوش و به 4 دسته تست خمش-تست کشش- تست ضربه و تست شکست تقسیم بندی می شود.
در تست مخرب قطعه مورد نظر آسیب می بیند یا می شکند، بنابراین قطعه قابلیت استفاده مجدد را نخواهد داشت.
چون زمان تست مخرب ابعاد یا ترکیب شیمیایی قطعه تغییر می کند.
در صنایع مختلف، تست مخرب جوش وقتی قابل توجیه است که یک قطعه در مقیاس انبوه تولید می شود.
از بین رفتن تعداد کمی از نمونه ها به منظور کنترل کیفیت مشکلی ایجاد نخواهد کرد.
تست کشش
تست کشش که با نام تست تنش نیز شناخته می شود، ساده، ارزان و استاندارد است.
چون با کشش ماده، می توان سریع واکنش آن را در برابر نیروهای اعمالی در شرایط کاری تعیین کرد.
از این تست مخرب جوش می توان استحکام کششی، مقاومت تسلیم، مدول الاستیسیته و انعطاف پذیری یا درصد تغییر طول نسبی و درصد تغییر سطح نسبی را به دست آورد.
تست ضربه
تست ضربه یکی از روش های استاندارد تست مخرب جوش برای تعیین انرژی شکست مواد در اثر تنش دینامیکی است.
تعیین مقدار انرژی لازم برای شکستن قطعه در اثر ضربه با این تست مشخص انجام می شود.
تست شکست
در تست شکست یا تست فشار جوش معمولا برای بررسی کیفیت مواد ترد مانند چدن، آلیاژهای ترد و هم چنین مواد غیرفلزی که تحت شرایط کاری بیشتر تحت تاثیر نیروهای فشاری قرار خواهند گرفت، کاربرد دارد.
تست خمش
در روش تست خمش برای ارزیابی خواص مکانیکی مواد کاربرد دارد و در آن مقاومت قطعه در برابر خم شدگی مورد سنجش قرار می گیرد.
این تست توسط دستگاه تست کشش یونیورسال و به دو صورت سه نقطه ای و چهار نقطه ای انجام می شود.
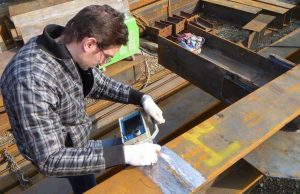
تست مخرب جوش
آزمایشی است که برای ارزیابی کیفیت و سلامت جوشکاری انجام می شود. در این تست، نمونه ای از جوش بریده شده و تحت آزمایش های مکانیکی قرار می گیرد تا مقاومت، چقرمگی و سایر خواص آن بررسی شود.
مراحل انجام تست جوش:
آماده سازی نمونه:
نمونه ای از جوش به ابعاد و شکل مناسب از قطعه مورد نظر بریده می شود.
سطح نمونه باید صاف و عاری از هرگونه عیب و نقص باشد.
انجام آزمایش:
از نمونه برای انجام آزمایش های مختلف مکانیکی مانند تست کشش، تست خمش، تست ضربه و تست سختی سنجی استفاده می شود.
در هر آزمایش، نیروی مشخصی به نمونه اعمال می شود و رفتار و عملکرد آن تحت این نیرو ثبت می شود.
تجزیه و تحلیل نتایج:
نتایج آزمایش ها با استانداردهای مربوطه مقایسه می شود.
اگر نتایج مطابق با استانداردها باشد، نشان دهنده ی این است که جوش از کیفیت و سلامت قابل قبولی برخوردار است.
در غیر این صورت، جوش معیوب تلقی شده و باید دوباره جوشکاری شود.
کاربرد های این آزمایش
کنترل کیفیت جوشکاری: برای اطمینان از کیفیت و سلامت جوشکاری در سازه های مختلف مانند پل ها، ساختمان ها، لوله ها و مخازن
بررسی روش های جوشکاری جدید: برای ارزیابی کیفیت و عملکرد روش های جدید جوشکاری
عیب یابی جوشکاری: برای شناسایی عیوب و نواقص در جوشکاری
تحقیقات جوشکاری: برای مطالعه ی رفتار و عملکرد جوشکاری تحت شرایط مختلف
مزایا
ارائه اطلاعات دقیق و قابل اعتماد در مورد کیفیت و سلامت جوش
امکان شناسایی عیوب و نواقص در جوشکاری
قابلیت استفاده برای طیف وسیعی از مواد و سازه ها
معایب
نمونه مورد آزمایش از بین می رود و غیرقابل استفاده می شود.
انجام تست زمان بر و پرهزینه است.
در برخی موارد، تهیه نمونه از قطعه مورد نظر دشوار است.
در تست های مخرب و غیر مخرب باید به نکات بالا (مزایا و معایب) توجه ویژه ای داشت و بر اساس بودجه و تناسب کار عمل نمود.

انتخاب بین تست های مخرب و غیر مخرب
انتخاب بین تست مخرب و غیر مخرب به عوامل مختلفی از جمله نوع ماده، نوع سازه، الزامات کیفی و بودجه پروژه بستگی دارد. به طور کلی، تست های غیر مخرب در اولویت قرار دارند، زیرا به نمونه آسیب نمی رسانند. با این حال، در برخی موارد ممکن است لازم باشد از تست های مخرب برای تأیید نتایج تست های غیر مخرب یا برای به دست آوردن اطلاعات دقیق تر استفاده شود.
استاندارد تست جوش
استاندارد تست جوش براساس آیین نامه ای تعیین می شود که سازمان نظام مهندسی برای ساخت و ساز کشور و کاربری مهندس ناظر پروژه منتشر کرده است.
طبق مبحث دهم مقررات ملی ساختمان و در آیین نامه ۲۸۰۰، الزامات مورد نیاز برای ساخت سازه فلزی، موارد زیر هستند:
استفاده از کارگاه برای ساخت سازه
استفاده از جوشکار ماهر
آزمایش تست جوش
آزمایش های داخلیتست جوش رادیوگرافی
تست جوش آلتراسونیک
فرآیند جوشکاری مانند سایر پروژه های صنعتی دارای اصول و استاندارد مشخصی است و برای کنترل دقیق قطعات جوشکاری شده استاندارد تست جوش در نظر گرفته می شود.
برای اطمینان از درستی انجام جوشکاری براساس استانداردها و دستورالعمل های مشخص روی اتصالات جوش شده بازرسی جوش انجام می شود.
اهداف کنترل کیفیت و بازرسی سازه های فلزی و تست جوش
بازرسی های لازم از قبیل کنترل ابعادی ، جوش ، پیچ و مهره ، رنگ ، لمینیشن و … که با توجه به نوع کار انجام شده از قبیل سازه های ساختمانی و یا پایپینگ و با توجه به درخواست کارفرما و استانداردهای مربوطه به هر آیتم تستهای مورد نظر صورت میگیرد و نتایج آن به صورت مکتوب به جهت حصول اطمینان ارائه میگردد .
بازرسی یک پروژه فلزی به جهت حصول اطمینان از کیفیت تست جوش شامل 3 مرحله می باشد:
1- بازرسی قبل از جوشکاری
2- بازرسی در حین جوشکاری
3- بازرسی بعد از جوشکاری
منابع: تتا– دیدبان سنجش امیرکبیر – یکتا خاک